|
COATING SERVICES
Our daily
general-purpose coatings are TiN, TiCN, TiAlCN (MP), TiAlN, TiAlCrN, CrN,
ZrN and more advanced coatings such as multilayers, Nano size, Nano grains
Coatings (similare to Alcrona/Alcrona pro), Naco, Nacro, Nacvic and our
own patented coatings including Nexcel, Nexgen, Nexvic, Extech, Ultimax,
and Nextech. The last six coating are high performance high hardness along
with high toughness properties and possess extreme erosion and corrosion
resistance. The last four named coatings are USA Patented coatings and
the patent rights has been assigned to Plasma Coating Technologies Inc.
There are
also three (3) coatings which are TRADEMARKED and assigned to Plasma Coating
Technologies Inc and are described below.
NEXGENNEXCEL:
This coating is the most suitable for machining, drilling and finishing
for Titanium and Titanium alloys. This coating will increase the tools
life at least by 10 times in comparison to uncoated cutting tools. This
coating also provides better surface finish and reduces considerable amount
of machine downtime. (Download
PDF file.)
NEXTECHNEXVIC:
This coating is the most suitable for machining and finishing of Aluminum
alloys. It will prevent long chip formation as well as sticking of chip
to the cutting tools. However, it can also perform excellent for machining,
cutting, drilling and finishing of stainless steels and nickel base super
alloys. (Download PDF file.)
NANOMULTICOATPRO:
This coating is used for machining and drilling of all types of composite
materials such as PMC, CMC and C-C composite. It is highly recommended
that suitable thickness of coating must be deposited on cutting and drilling
tools depending upon different types of composite materials being machined.
For example for polymer matrix composite and Carbon-Carbon Composite (C-C)
machining, generally coating thickness must be in the range of 12-15microns
in thickness for optimum performance of cutting tools.
(Download PDF file.)
In Table I, we have listed mainly general-purpose coatings and their properties
and maximum temperature that are used for these coatings; However, this
information is provided for reference purposes only. The Coating
Properties generally varies due to Thickness, Rotation of speed, Deposition
Temperature, Chemical Compositions, Grain Size, total Numbers and Size
of coating layers, ratio of reactive gases and applicable environment
and temperatures.
Click
Photos to Enlarge
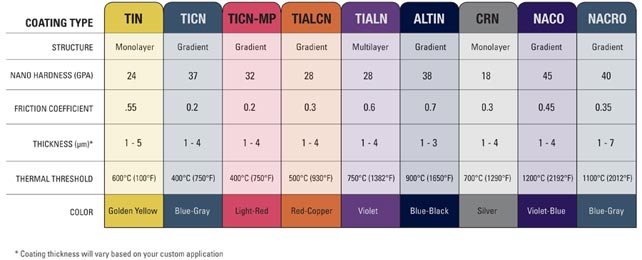
|
|
|
|